Balancing Schemes
A typical assembly line consists of an enumeration of work centers where assembly tasks (=operation steps, the smallest undividable amount of work) are performed. Depending on the complexity of the end items that need to be build and the available manpower, the tasks can be balanced among the available work centers. Each operation step has its typical duration and the goal is to distribute the operation steps among the work centers to obtain equal takt times for each work area.
Takt time is the total available production time divided by the average customer demand. The takt time is the available time to produce one item.
Within Objective it is possible to setup balancing schemes. A balancing scheme defines the takt time and can be applied to a resource group (production line, assembly line,...).
In a balanced production line, operators can continue working without interruptions, which ensures maximum efficiency.
Example:
An operation consists of 4 subsequent operation steps. The takt time is 10 min (every 10 min, an item will be produced), but operator 2 and 3 will have to wait 5 min per cycle, which is not efficient.
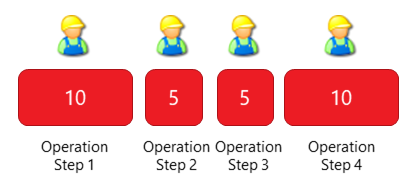
A possible solution to balance this production line is working with 2 operators and a takt time of 15 min:
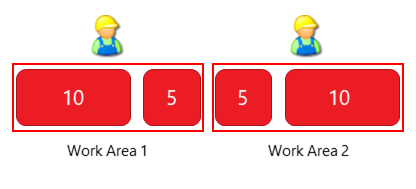
If a faster takt time is required, the production line can be rebalanced in the following way:
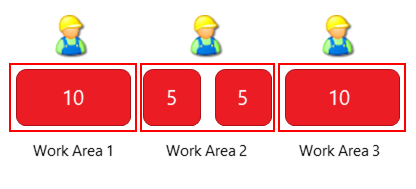
In the Supervisor, multiple balancing schemes can be set up with different valid time intervals, when e.g. the demand for a certain item varies throughout the year. Instructions and instruction sheets can be added for every single operation step.